Internal Combustion Engine
The Beating Heart of the Mercedes-AMG ONE
The Internal Combustion Engine, or ICE, is the beating heart of the AMG ONE. The team working on this fantastic machine has had to overcome many obstacles to bring it into existence. Melding high performance, high efficiency, and meeting street-legal standards for emissions, noise regulations, and safety has been a journey all its own, along with making this vehicle able to sustain running laps on the track or running down to the local shop.
Breathtaking innovations, a masterpiece of engineering and ultimate performance: Take a look inside what powers the beast that is the Mercedes-AMG ONE, a fascinating vehicle with the soul of an F1 car like no other machine on the road to date.
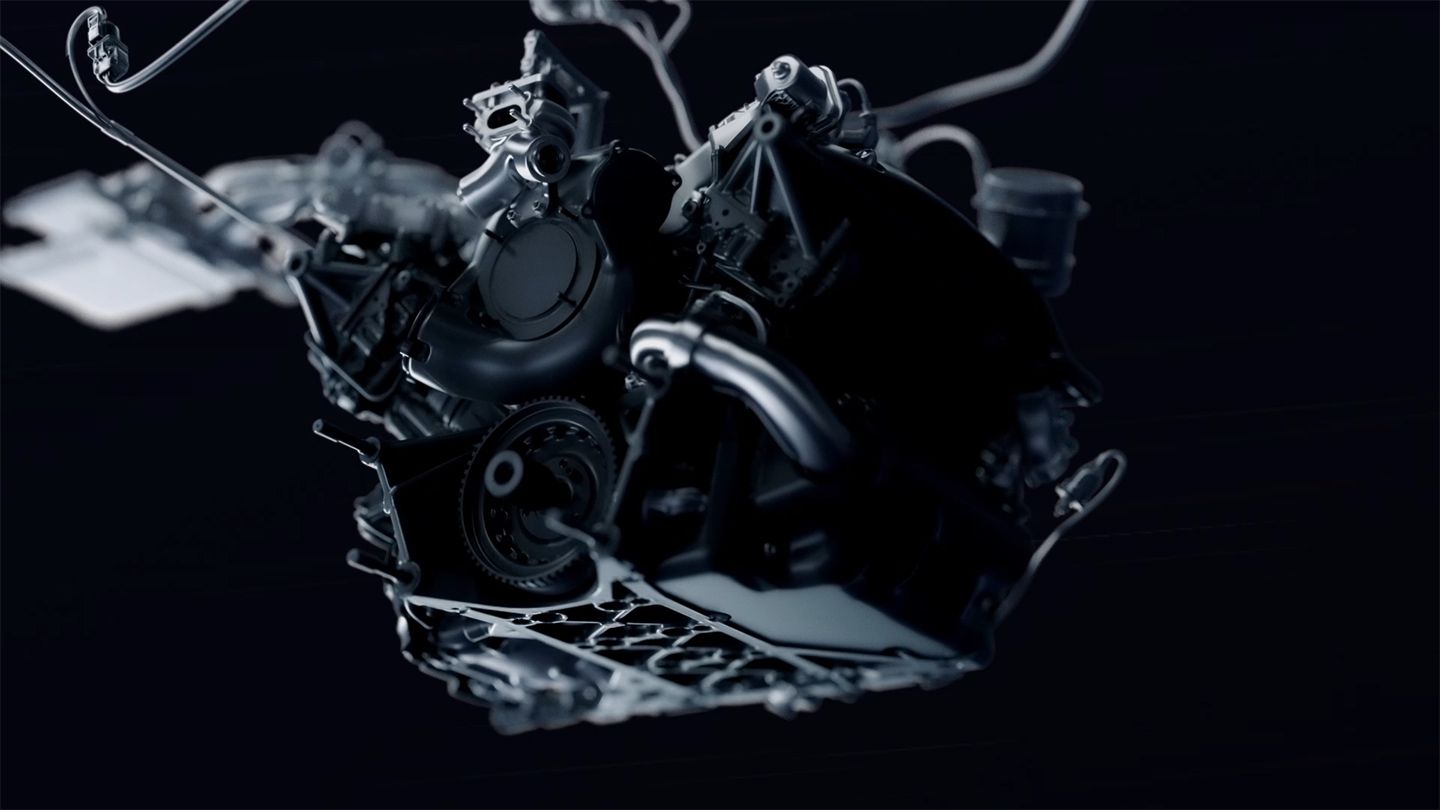
Technical Facts
Heart of the Mercedes-AMG ONE Internal Combustion Engine
- MGU-H RPM 100,000
- MGU-K RPM 36,000
- MGUFs RPM 50,000 at vMax
- System Performance 782 kW (1,063 HP)
- Lifespan in Kilometres 50,000
Adam Allsopp, Project ONE Powertrain Director at Mercedes-AMG High Performance Powertrains, has made it his personal mission to make the impossible, possible. We spoke to him about the most significant technical aspects of the AMG ONE’s Internal Combustion Engine and the components that comprise this, in his words, ‘car that is totally different to anything I’ve driven before’.
This was an enormous undertaking on all fronts with a team who had been in the business of designing machines to race and who had never done this before.
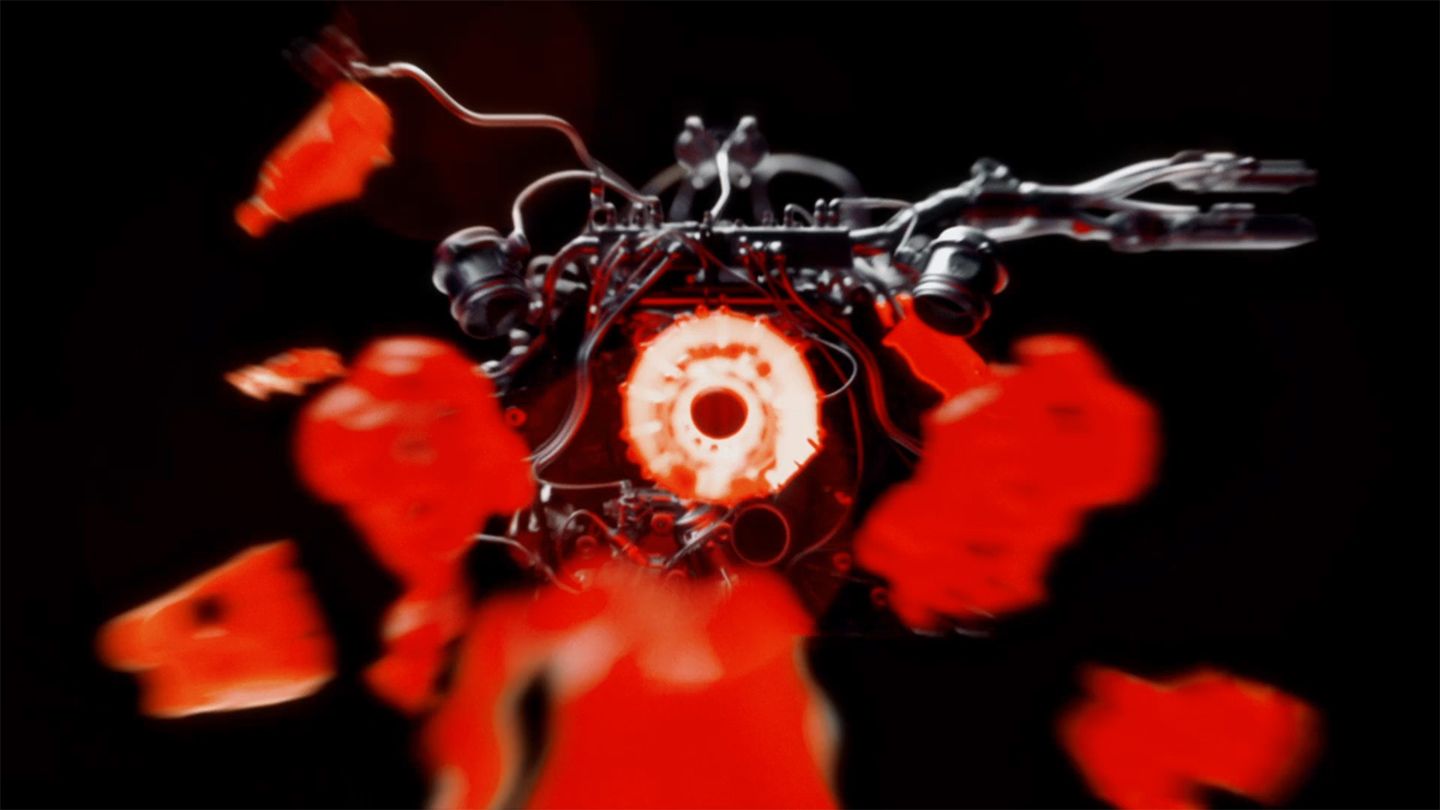
Can you tell us about how proud you are of this engine and what is the most exciting fact about it?
Our team is extremely proud of this engine. No one else has been able to take a Formula 1 engine, a machine intended to win races by achieving the highest efficiency and power output, without regard to emissions or noise, and adapt it so that it meets all the prerequisites for driving on public streets. We have reached the final stages of making this happen.
What was your overall focus in developing the ICE?
Our primary focus was to make this engine more durable than that of a classical racecar. A Formula 1 engine can only withstand a few races before needing to be replaced. Currently our engine lasts 31,000 km. Both the ICE and the electric motors were adapted, but the technical principle of the Formula 1 car is still intact. The ICE is more or less exactly the same. After this, our next hurdle was particulate emissions. A Formula 1 engine produces high emissions without a catalyst and filter, and gaseous emissions play a role here as well. We optimized combustion with high charge motion in-cylinder, along with in-cylinder vaporization, added a second, port fuel injection system, and the latest in filter and catalyst technology in order to reach the correct levels.
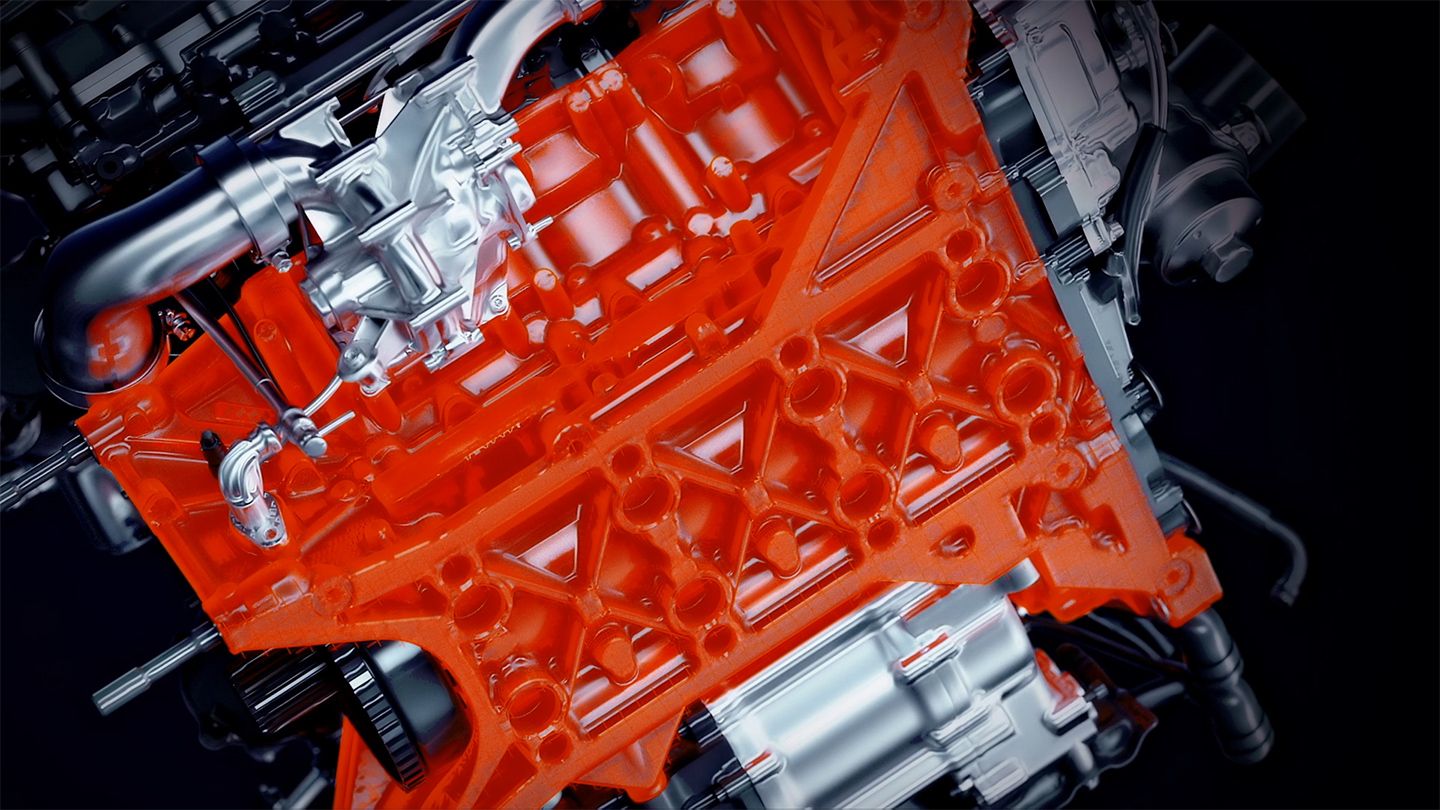
It was a tough road to get to where we are, but I think we’re in very good shape at this point. Distribution and mixture preparation were improved by putting a large amount of fuel into the combustion chamber via the GDI system and then applying the second, port fuel injection on the other side of the cylinder head. This, along with optimized airflow, slightly smaller ports, and the use of the latest in after-treatment, really made the difference. Though these alterations had some effect on the maximum power output of the engine, we’re still at an extremely high level. Catalysts are also pre-heated before the engine even starts using 16 kilowatts of electrical energy in heated catalysts and then using the three-way principle, which results in very good performance concerning gaseous emissions. Innovative filtration technology is implemented after this point, resulting in better emissions under all conditions, including Real Driving Emissions.
What were the greatest triumphs during development and implementation in the AMG ONE? What were the biggest technical challenges in the development of this engine?
The greatest challenge for us, overall, was taking a racing engine and making it drivable and usable not only on the track, but also able to handle a traffic-jam. For comparison, a Formula 1 car idles at a speed of 4,000-5,000 RPM – this is not doable in an urban setting. Not only is it far too noisy, it would also lead to higher emissions under normal, urban driving conditions. The addition of the electrical front axle also assured that a driver could operate the vehicle in a city without issues and under any conditions. Crash tests and safety requirements were another challenge we have faced that was different to working with a Formula 1, purely racing-focused engine.
This was an enormous undertaking on all fronts with a team who had been in the business of designing machines to race and who had never done this before. One of the greatest triumphs we’ve experienced was receiving pass-by testing certification. I’m very happy with where the results are now and where we’re headed. On top of this, we’ve broken the unofficial lap record for a public road car on a UK racetrack by two seconds within the first testing day. The positive feedback we’ve received from drivers, that this car is not only amazingly quick, but that it’s easy to drive as well, is also a massive triumph for us.
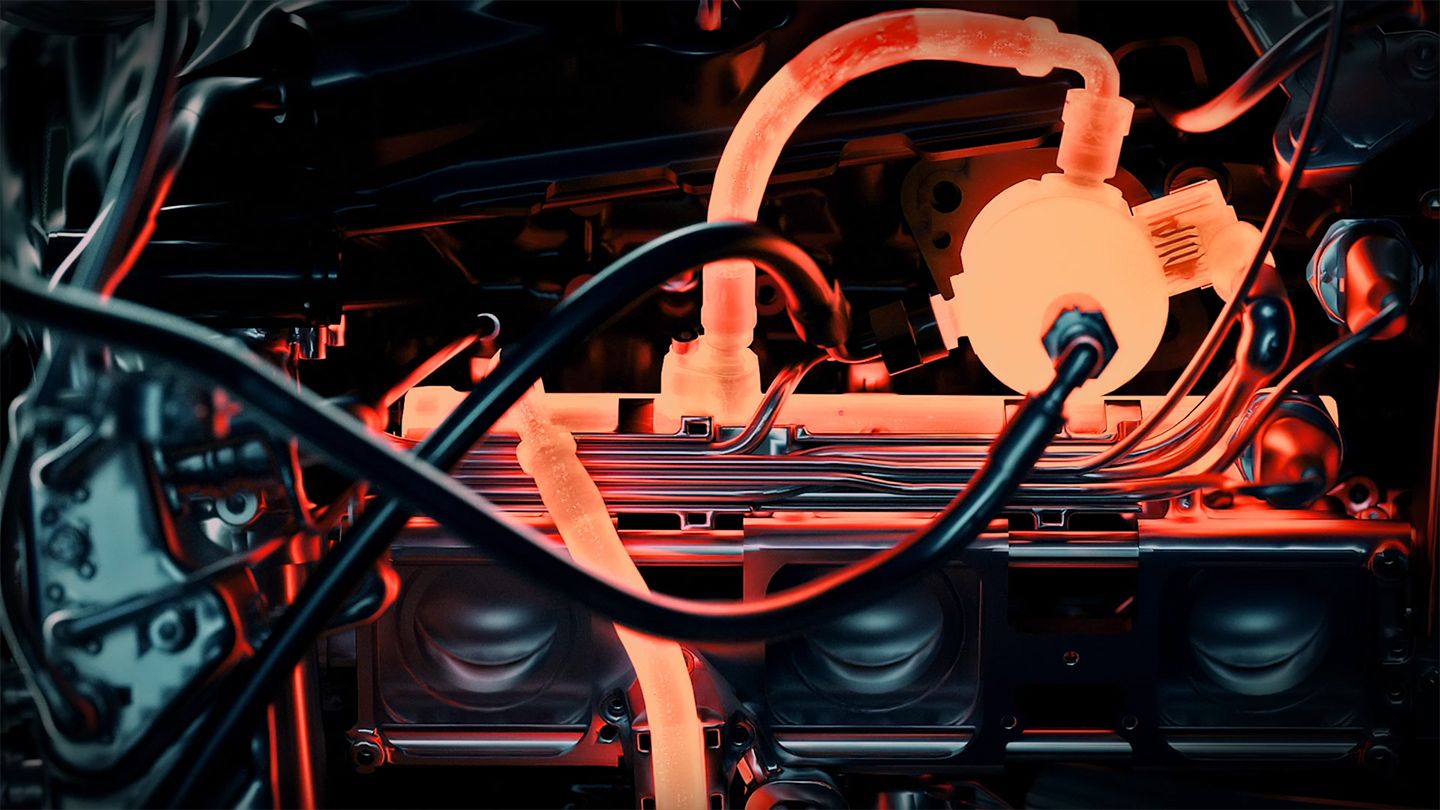
We know that this engine is nearly a complete translation of a 2016 Formula 1 engine. Nevertheless, some changes had to be made to the engine to make it roadworthy. Where does it differ the most?
Yes, the engine is mostly the same as the 2016 Formula 1 engine, but to achieve the target mileage we had to reduce the compression ratio or strengthen the crankcase, for example. However, the heart of the Formula 1 engine has remained the same – that is also the purpose of this vehicle. There are also other components that we have added, such as port injection or the electrically heated catalyst. This is the only car on the road that has a pneumatic valve train, plus we've added a pneumatic pump. In order to reach the NVH (Noise Vibration Harshness) level, small changes have also been made to the gear train between the crankshaft and camshaft. Despite the additions, the similarities with the Formula 1 engine are unmistakable.
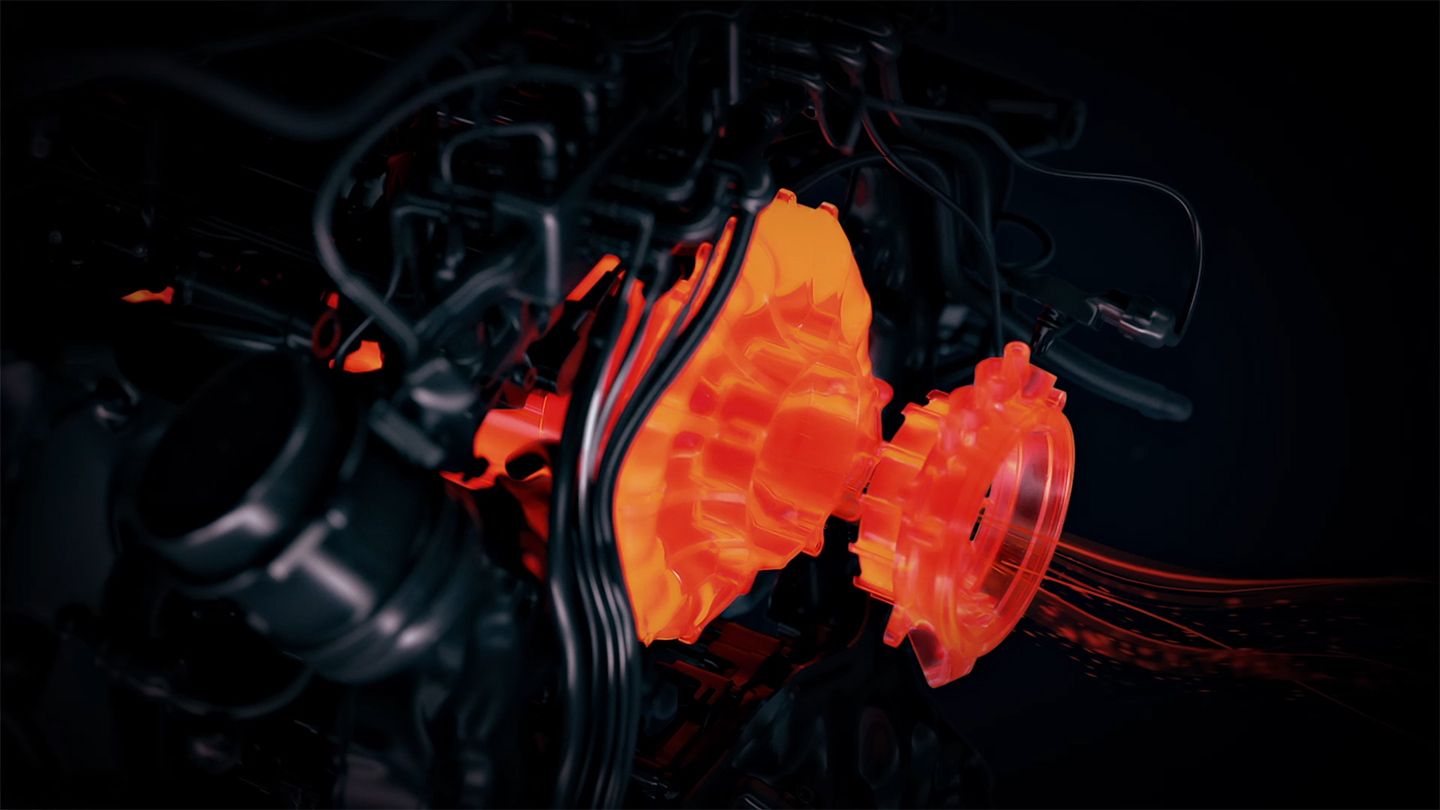
Could you tell us about some particular components in this engine you would like to highlight and why? What are their effects on driving dynamics and what’s innovative about them?
There is no car on the road running with a pneumatic valve train. It allows the engine to run at extremely high revs, around 11,000. A F1 racecar can go higher, but you have to respect the abilities and boundaries of components like the gearbox and others, that’s why we’ve capped it. Revving up to 7,000 RPM with the turbocharger already feels amazing; above 7,000 RPM it feels like an explosion of power. The turbocharger, or MGUH, produces an extreme boost to the engine with around 80 kilowatts of power while also harvesting energy for the battery and driving the electric motors.
This is one of the most fantastic features because it’s a combination of an enabler of high power output and high efficiency in one. Thermal energy is put back into use from the exhaust. The MGUK is integral in feeding additional power to the rear axle, along with the electrical front axle, which has inputs of 120 kilowatts on each side. All of these components work together to allow the vehicle to drive in either EV mode, or a combination of EV and rear axle modes. The hybrid system and ICE together amount to a system output of over 1,000 horsepower. Our front axle also has a very positive effect on vehicle dynamics via torque vectoring. This is a wonderful tool for steering and especially for cornering.
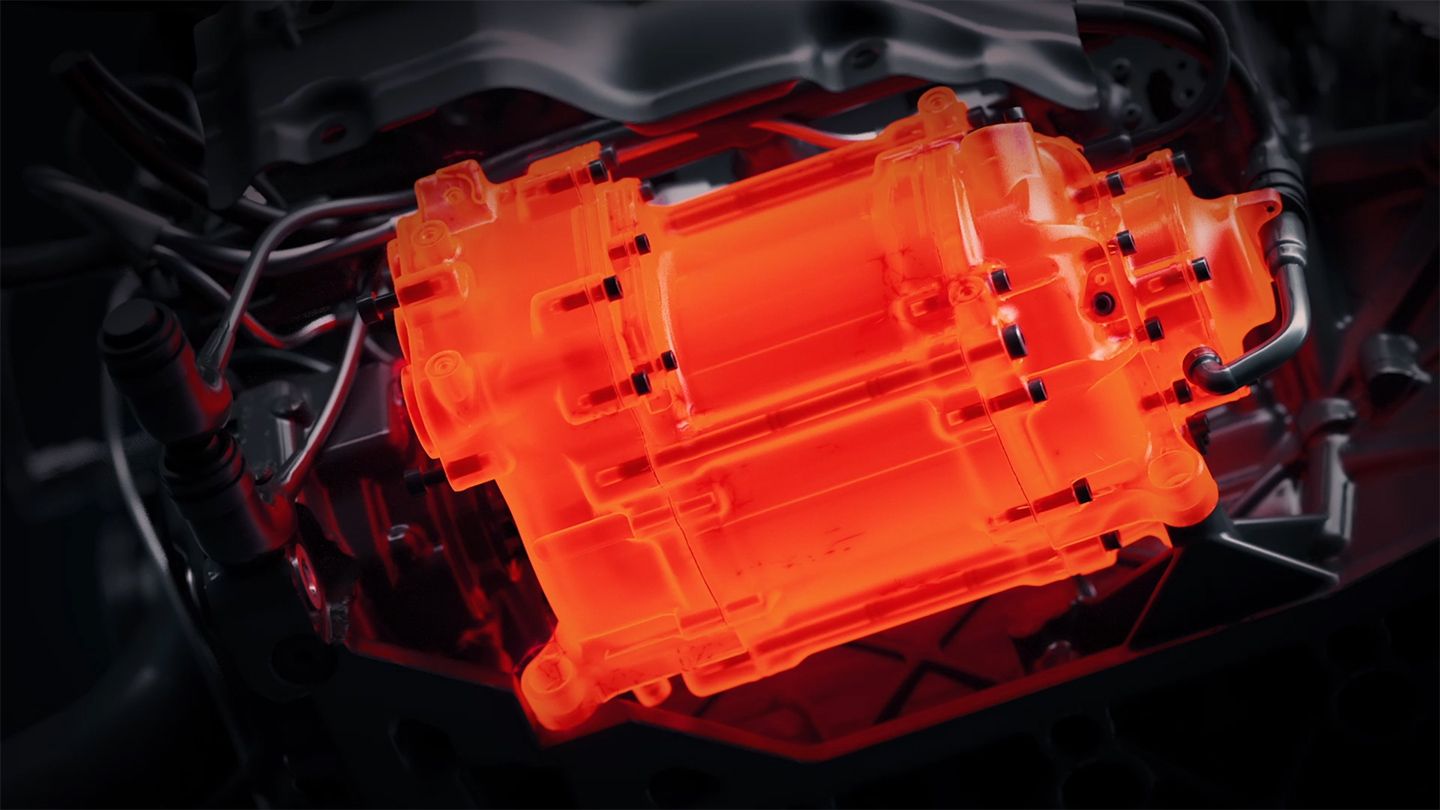
This is the first time an electrical turbocharger has been implemented in a road car, could you tell us a little bit about the development of this component, its effects, and how you achieved this?
A turbocharger is not common to see currently in road cars as this component is normally reserved for F1 racing engines. With temperatures up to 1,000 degrees are produced by the combustion process and then pushed through the turbine, it’s not an easy component to implement. On the other side of this is the relatively cool compressor, and between them is the electric motor, which doesn’t do well with extreme heat. Because of these complications, a turbocharger running at high speeds, up to 100,000 RPM, has thus far only been used in Formula 1. Along with this, CO2 emissions must be taken into account, as well as legislation, and penalties if limits are not adhered to as an OEM. We started this adventure into producing this machine at larger scales and achieving this level of efficiency in such a powerful engine with these prerequisites.
We optimized in order to increase boost level without affecting drivability. Usually, the turbocharger is only driven by the exhaust flow, meaning that there is always a lag if you have a tip-in as a driver. Boost pressure must first be created by the power of the turbine transferred to the compressor. In this case, the electric motor spins up the turbocharger to create enough boost pressure on the intake side, thus producing immediate power. A tip-in means receiving a high boost level which has a positive, dynamic effect on the drivability of the car. Efficiency is increased as the turbine acts as a generator for the electric motor by using thermal energy that would normally be wasted. This energy is fed to the front axle or to the battery instead of only producing hot exhaust gas.
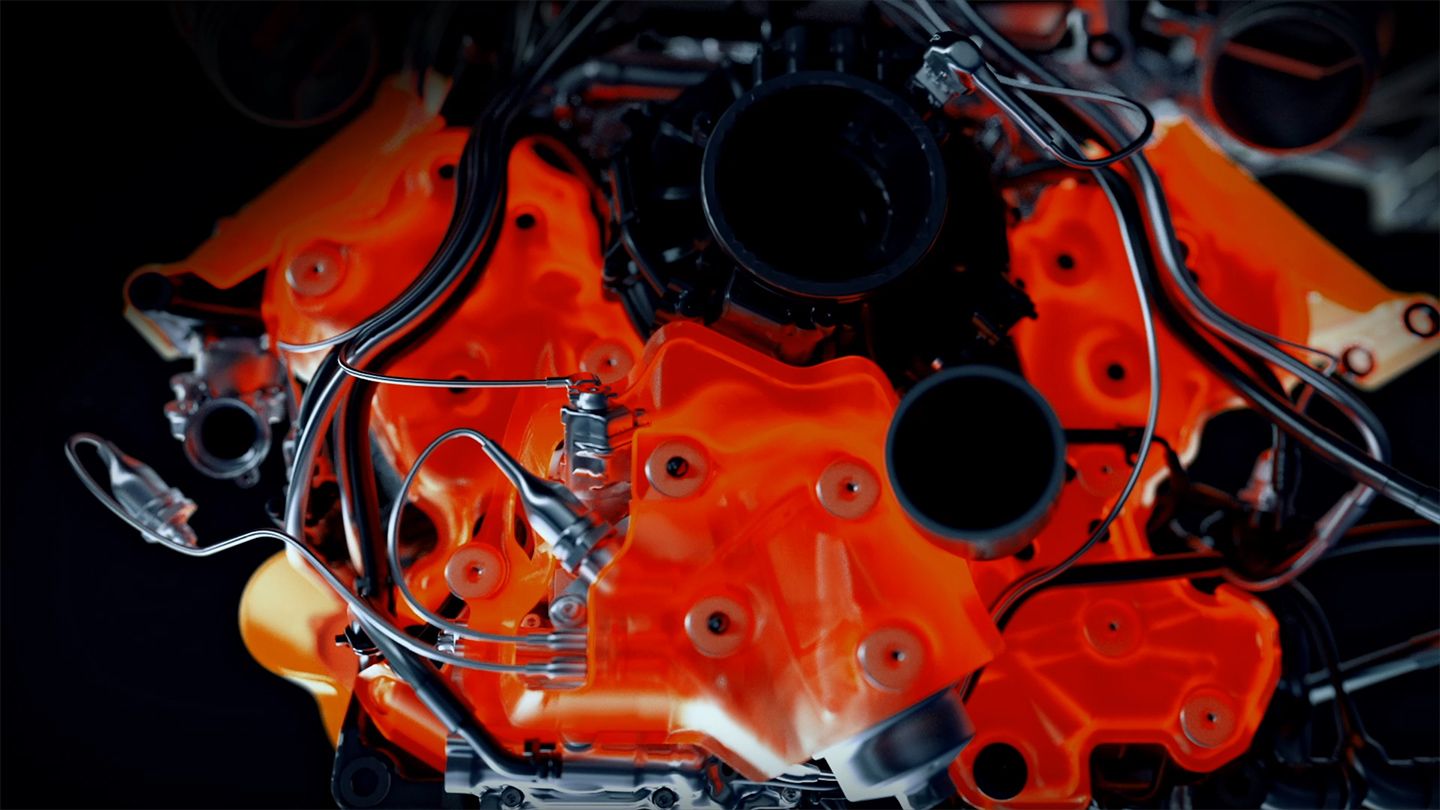
I don’t think that this construction is specifically unique, but I do believe that it will become more and more relevant for high powered sports car designs as the need to achieve higher efficiency grows. This usually occurs through downsizing the engine. In the past, AMG produced an eight-cylinder natural aspirated engine with 6.3 liter displacement, now we have 4 liter displacement, and who knows where the future will take us? This is a boosted engine, an actual eight-cylinder with 4 liter displacement, with higher power and torque output than its 6.3 liter predecessor. An electric turbocharger is vital as we progress in making engines more compact, more efficient, and even more powerful.
It’s really thrilling the first time out because it’s that quick. But it’s a lot of fun.
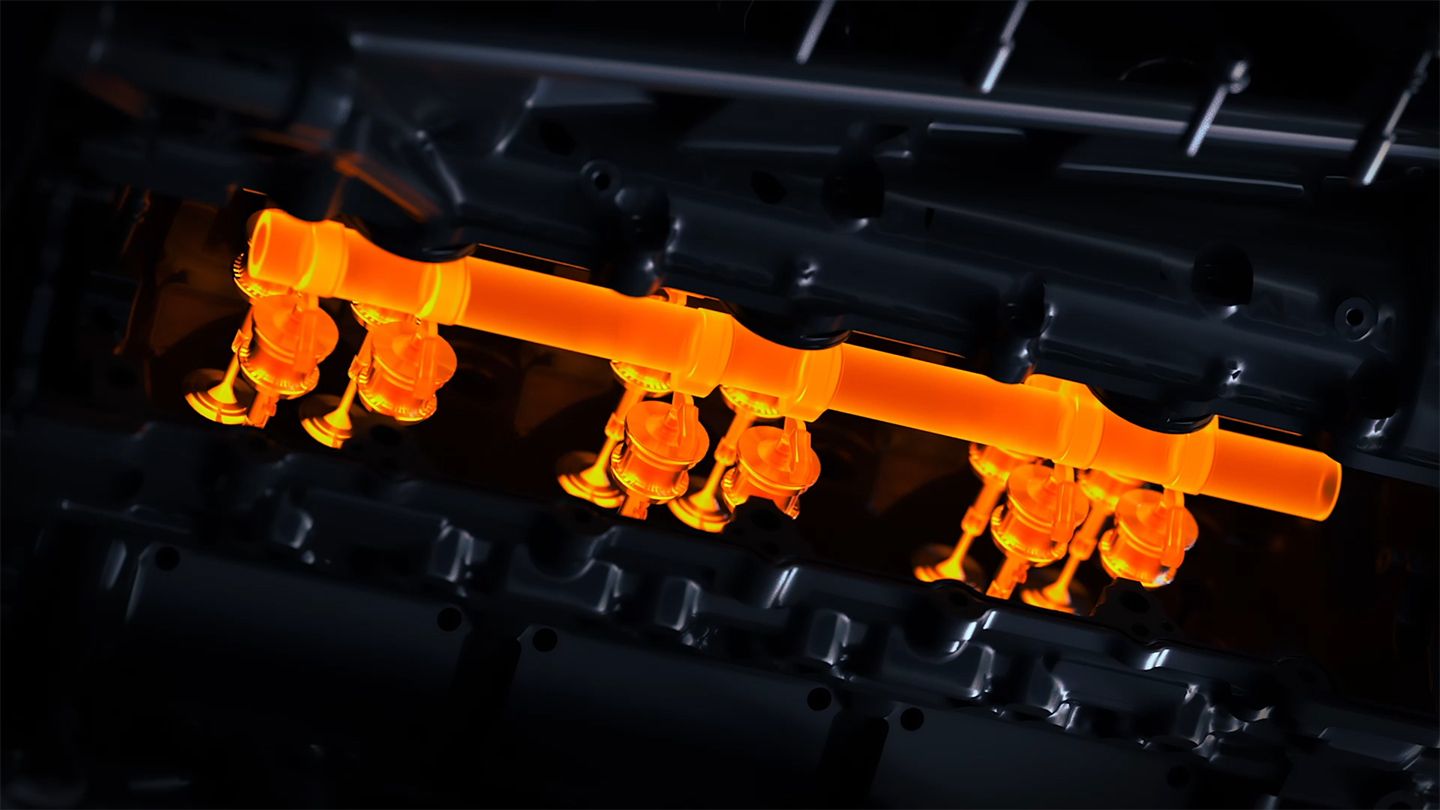
How does the pneumatic valve train affect driving specifically?
Though these components and materials are designed to operate under high intensities, we still have to respect their limits. The pneumatic valve train can reach 11,000 revs without compromising the cam profiles. Using a cam profile that provides fantastic power output, especially at high revs. This, as a classical sports car engine, puts linear or progressive power distribution over revs. This is a totally different car to anything I’ve driven before. It feels unbelievably powerful already revving at 6,000. It’s really thrilling the first time out because it’s that quick. But it’s a lot of fun.
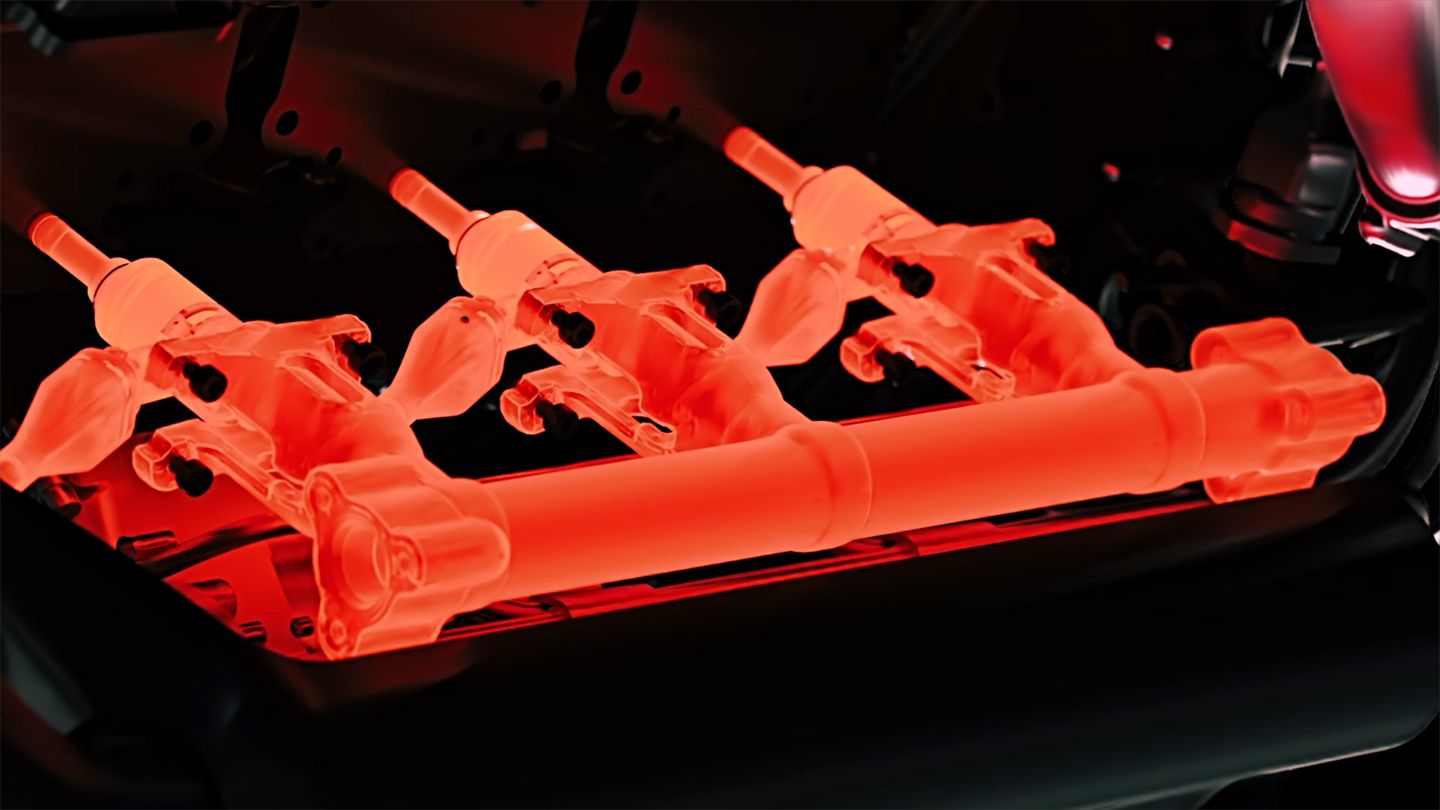
This is the first ICE in a street-legal car directly coupled with a 120kW electric motor, what were the greatest challenges in its implementation and why hasn’t it been done before? What are its specific benefits?
This 120-kilowatt electric motor is directly based on the Formula 1 engine and is completely different to any design normally done in mass production. When mass produced, this is usually directly attached to the crank. In this case, they run at the same speed in order to gain high low-end torque. The electric motor in a standard BEV is most impressive at the first launch of the car. In motor sports, this doesn’t matter as much; a high rev range that creates power geared toward performance is more the focus. These motors are designed for different means.
In a Mercedes road car with a hybrid engine that runs at 7,000 RPM, the electric motor would also be running at the same rate – 7,000 RPM. Our electric motor, the MGUK, is running at more than 30,000 RPM and creates maximum power at higher speeds, not just from zero. The electric motor offers very sporty power distribution in regard to revolutions. Its big advantage is the combination of the electric motor with a high-rev concept, extremely high efficiency, and a gear train behind to couple it directly to the crank, resulting in a very light design. It looks a bit like the starter of a standard combustion engine. You would never imagine that the MGUK has a power output of 120 kilowatts. It's very, very small, and can be integrated completely into the ICE.
The basic idea is similar to a gas turbine as it produces high revs and high power density. We use exactly that concept also for the electric motors on the front axle where it revs up to over 50,000 RPM. This works in combination with one gear connected to the front axle to create the correct speed for each wheel. Maximum power is also produced in high speed conditions.
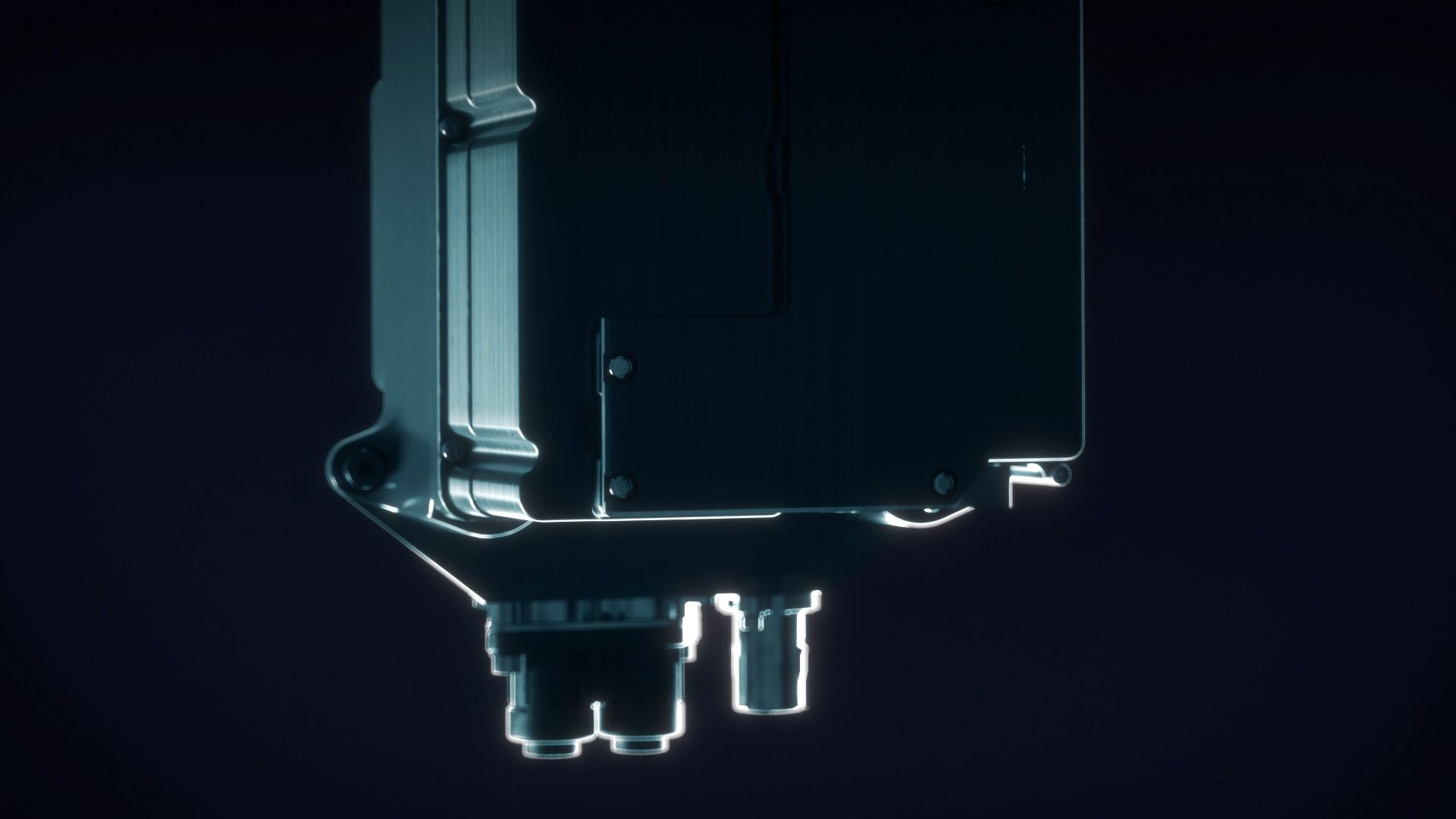
The Electrical Powerhouse of the Mercedes-AMG ONE
We spoke again with Adam Allsopp, Project ONE Powertrain Director, where he gave us an extensive look into AMG ONE’s hybrid system, how its powerful components come together, and how this electrifying vehicle generates such enormous amounts of power.
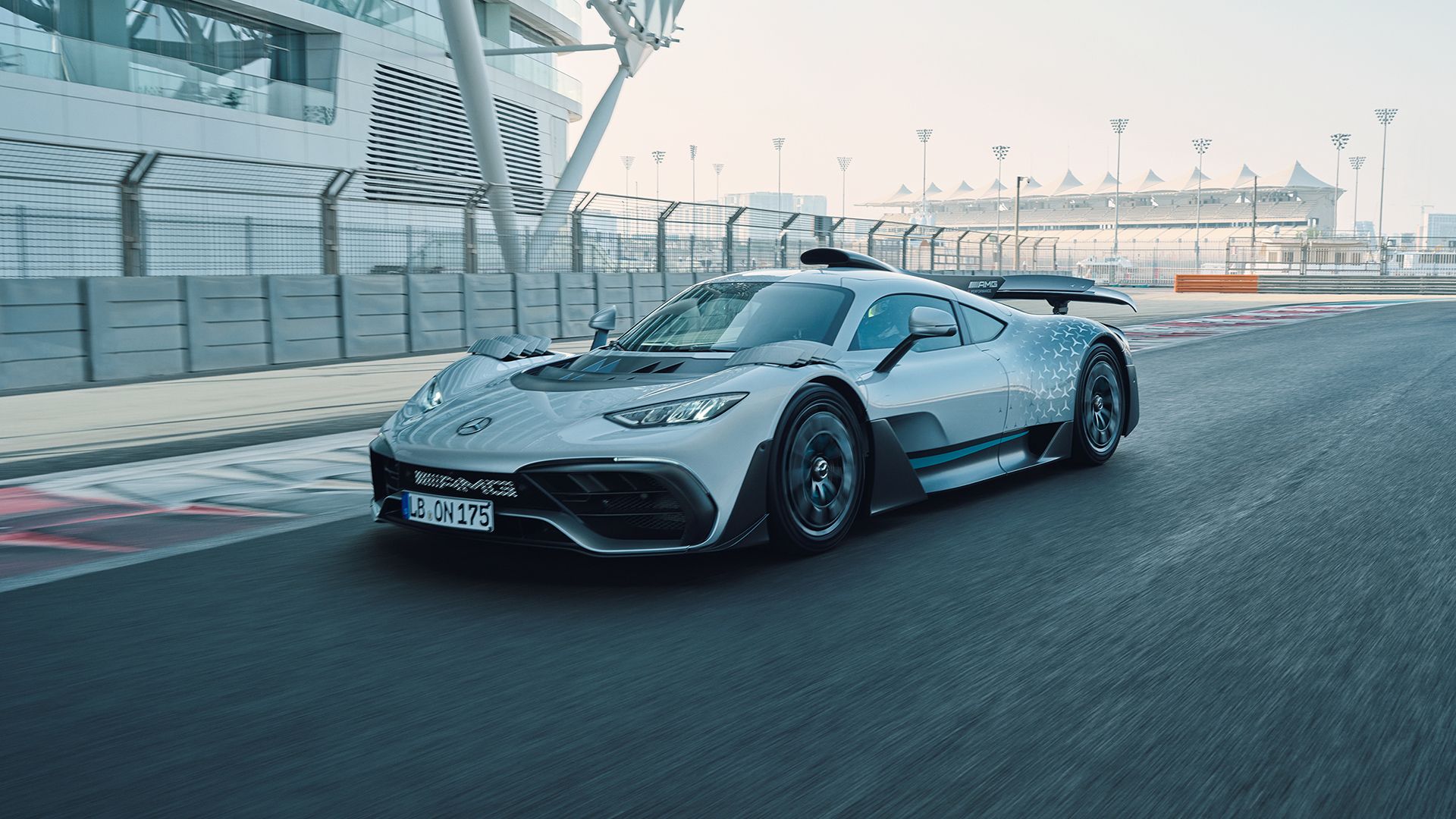
Mercedes-AMG ONE
Built to become a legend: the Mercedes-AMG ONE. The most extraordinary, contemporary, road-legal racing car to emerge from Affalterbach. Inspired by Formula 1, peppered with superlatives, made for the road.