Hybrid System
The Electrical Powerhouse of the Mercedes-AMG ONE
The Hybrid System of the Mercedes-AMG ONE is the great conductor of the electric current that binds and boosts this vehicle from front axle to rear exhaust. Along with the Internal Combustion Engine, these two systems work together to create the powerhouse of this extraordinary vehicle. If the ICE is the beating heart of the AMG ONE, then the Hybrid System represents its life force – clearly set on pure power and speed.
Join us for a look at the precise and excellent system that empowers the AMG ONE to reach new dimensions of speed, agility, and performance.
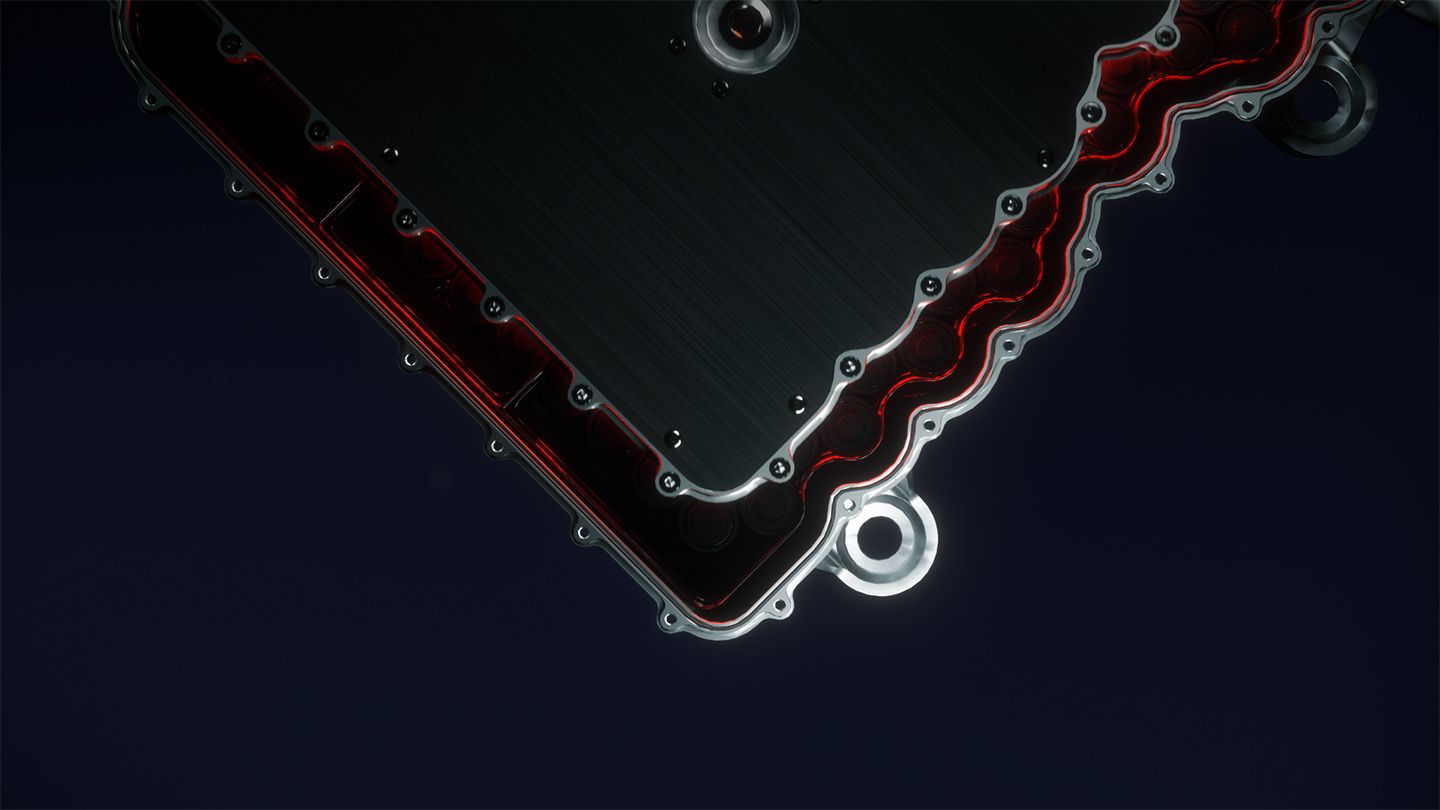
What are the biggest advantages of a hybrid system in general? What is especially beneficial for a hypercar like AMG ONE?
I see three major benefits; the first is efficiency. While harvesting energy during braking or using the MGUH, which is different to a standard hybrid powertrain, phlegmatization offers a mode for better efficiency. This means that the ICE can operate in a more efficient mapping area by splitting the torque between the MGUK and the ICE. Secondly, and more importantly, is the benefit of obtaining extra power for better driving dynamics using the three electric motors, which are very powerful compared to standard hybrids, in conjunction with the ICE. These enable for four-wheel drive and add other options in terms of vehicle driving dynamics. Last but not least, the electric motors are precisely controllable and are extremely dynamic in their behavior compared to those of a standard ICE. This allows for a high amount of control over this enormously dynamic car, combined with features like torque vectoring, which is a fantastic feature for drivers.
What were the main challenges in designing, creating, and implementing the hybrid system? What was the main focus for this system?
We could talk about this topic for hours, but the main challenge has been combining all of these components into this complex machine. We had to be sure that the results met the development targets. A standard power train has only two components: an ICE and a gearbox. This is somewhat of a standard process in the automotive industry and is thus relatively easy to put together.
The Mercedes-AMG ONE has a few additional components, not only in the ICE, but in the entire system. The internal combustion engine is made more complex with the addition of an MGUH - a highly sophisticated electric turbo charger - as well as the integrated electric motor, the MGUK. Everything had to be optimized in various dimensions. Our power unit needed to match the ICE and the gearbox. The battery, inverters and a couple of electric motors come into play. Each component has its own limits. The battery, as an example, has an optimal operational temperature of around 50ºC in contrast to an ICE, which operates optimally at above 80ºC. All the various limits and optimal operating conditions of these components had to come together to work within this space. The secret was then to solve that multi-dimensional equation to get the best compromise in terms of efficiency, power output, and weight as the most important dimensions, along with others.
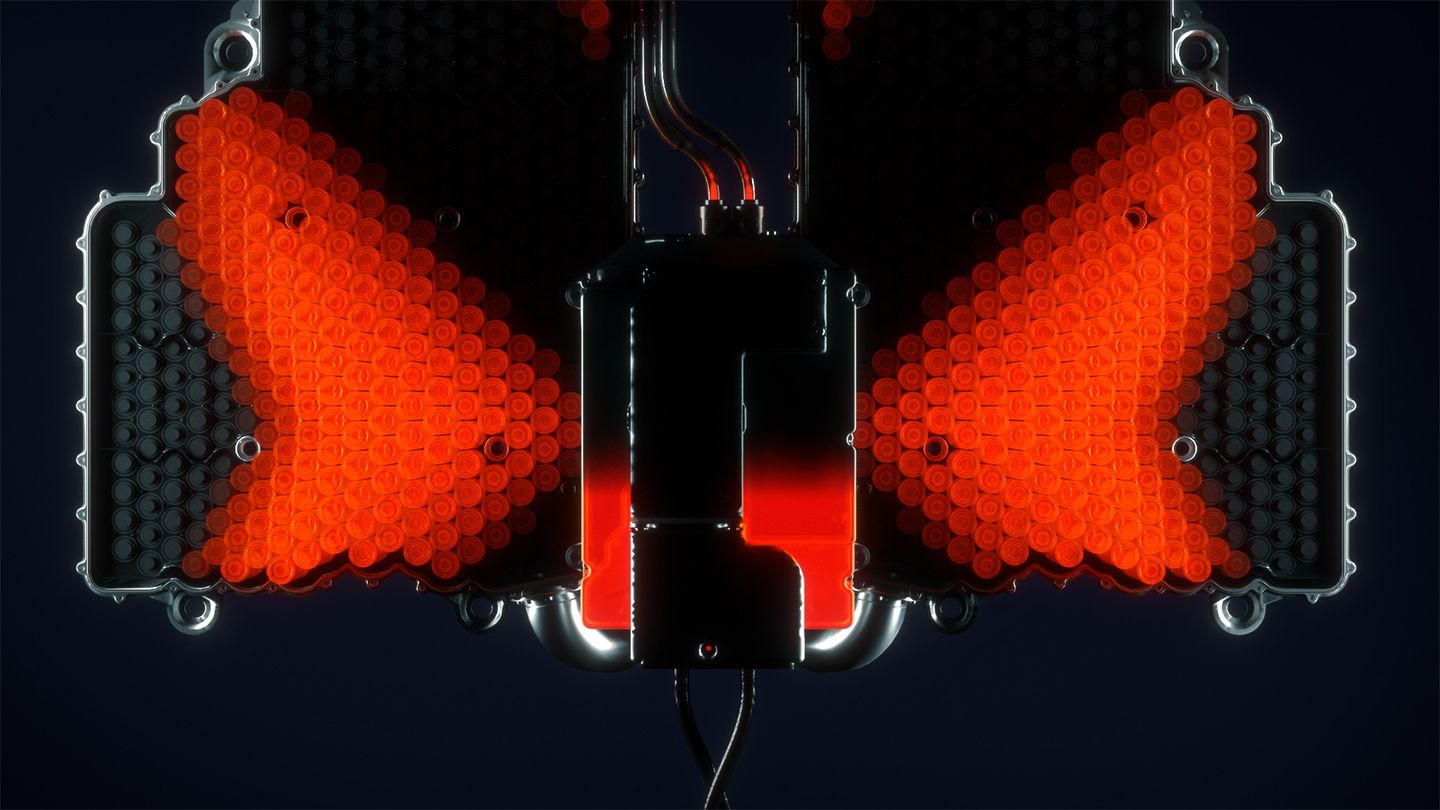
Could you tell us about the most significant points in this hybrid system? How do they compare to their F1 counterparts, if at all?
What’s most fascinating in this system is that it is nearly identical to an F1 System. It’s not a machine that is similar to an F1 engine.. The difference concerning the ICE is that we can’t run it lean because we have to stay within the emissions limits. We are running lambda = 1 mixture and we are using catalysts and filters to convert raw exhaust gas into “air”. The ICE and the rear axle operate in the same way as in Formula 1 with only minor changes related to emissions.

High efficiency is achieved through the electrically assisted turbocharger (MGUH), which provides high power output for the ICE by using a large turbine and compressor. This might normally feel ‘laggy’, but is supported by a strong electric motor. These work in conjunction to deliver dynamic boost pressure at a high pressure level thus ensuring the greatest specific power output.
These components are also a factor in harvesting exhaust energy and routing it to the MGUK, which can either provide extra power to the crank or harvest energy from it depending on the driving situation. The biggest difference to a F1 car is the electric front axle with its two electric motors. It’s more or less the same as the MGUK concept, but runs at higher speeds, up to 50,000 RPM, and works with a small gearbox to generate an extra 240 kW on the front axle. All these components can work independently from each other, meaning that the front axle can be used for torque vectoring, making the car more agile while cornering. This was first implemented in the AMG SLS Electric Drive and it feels fantastic when you’re behind the wheel.
We know that this battery system is more compact, as is the rest of the engine, than other high-powered hybrid systems – how was this achieved on a technical level?
Our development target was different to that of standard EVs, which normally have a battery optimized for range and every-day driving and usage in very low and very high temperature conditions. Our modified F1 battery is optimized for power output and performance on the track. These cells are different to a standard hybrid, but we’ve used the exact same technology from F1 and scaled it for the project. It’s 4-times bigger than the F1 battery. We have a power output that is much, much higher compared to standard EVs. The maximum power output of the battery is higher than 400 kilowatts, and 360 kW are applied directly to the street via the MGUK attached to the ICE and the two on the left and right sides of the front axle. The MGUH supports the ICE and works as an additional amplifier by delivering a high level of boost pressure so that this small 1.6 liter gasoline engine produces more than 400 kW of fuel combustion power from its main power source.
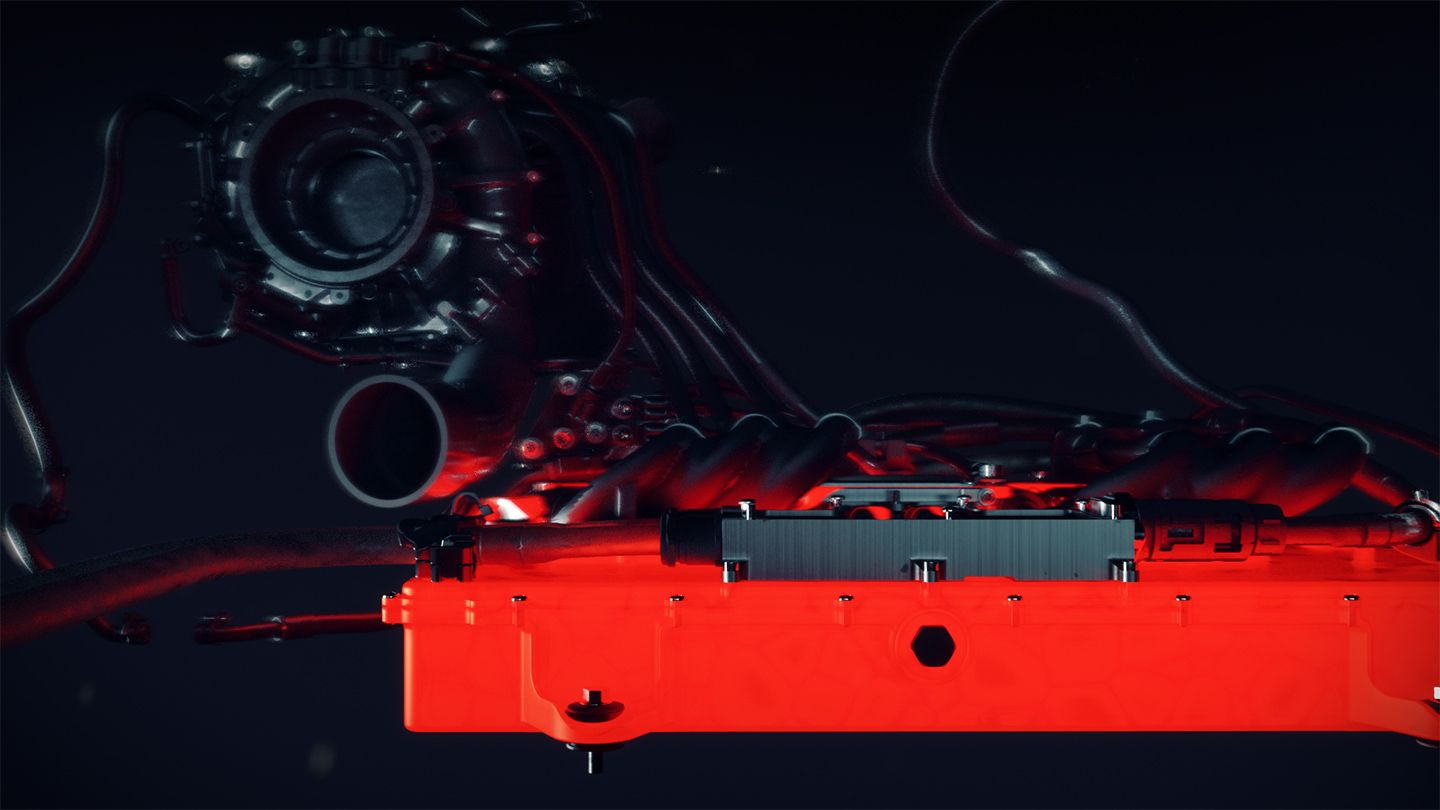
What is different about this battery setup compared to other street-legal hybrids? Will this system be seen in other road cars at any time in the future?
This is a complex question, but I'll try to answer it. This is a hybrid with electric drive capabilities that can also run in pure EV mode. In EV mode, it does not have the range of a standard EV, which is typically a couple of hundred kilometers. Our vehicle, of course, is not standard and this is not the purpose of our concept. This vehicle has the advantage that it’s geared for speed and efficiency, recuperating energy as the battery is drained and charged during driving. It is not dependent on a plug somewhere to recharge the battery, but it can still be plugged in to achieve a charge or be recharged. The battery is smaller compared to standard hybridsThis is a totally different concept with only one target: Maximum driving dynamics, maximum fun while driving, and reaching the next level of performance.
How were you able to achieve a higher power capacity than a Formula 1 battery at the same time as keeping all components compact?
This is a very good question. It was somewhat similar to a game of ‘Tetris’. We had to sort all the small bricks in a way that allowed for optimal packaging and placement. We scaled up the battery and tackled the most important obstacle, which was how to integrate that larger capacity into a car without compromising its function. We couldn’t reduce the size of the cells themselves, but we could package them in a different way. There were a lot of criteria we had to respect in order to accomplish this, not only concerning weight and packaging. This also included the very important task of cooling; again, a multidimensional equation, which has a lot to do with optimization. We have had some very clever engineers on the project who have helped in achieving this.
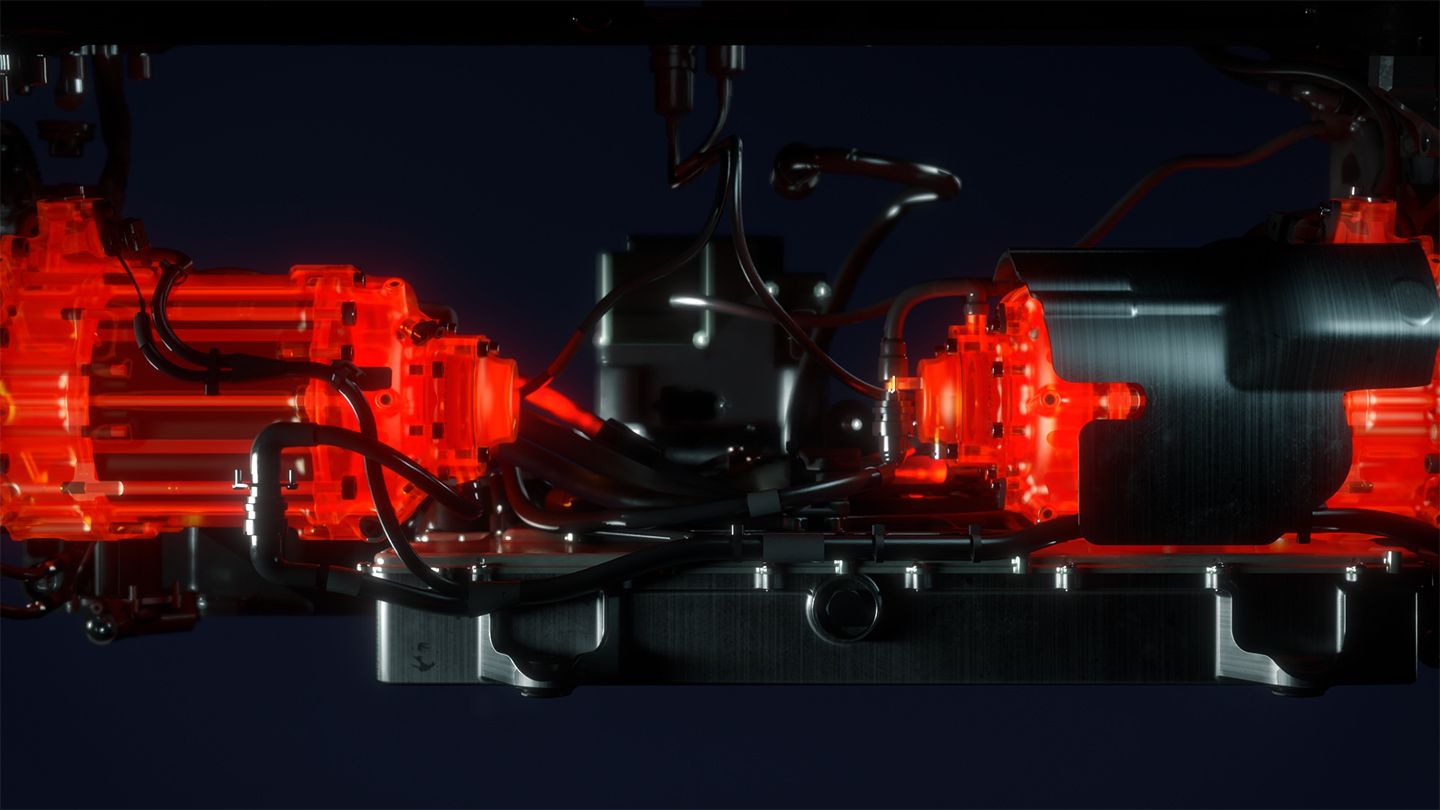
Could you tell us about the direct liquid cooling of the battery’s cells? Why is this the preferred method of cooling? How is this different to existing cooling systems?
It's a very complex system. The first focus for the design was the direct cooling of the batteries because the cells themselves are in direct contact with the coolant and most of the surface is in contact with the cooling liquid. Exactly the same as for F1. This is the most efficient way to remove heat from the cells while charging or depleting them. This is too complex for mass production and we are not in a position to mass produce this system, but it’s the best concept on a technical level for this project. Specific sealant concepts and production processes are necessary to ensure that it works safely and reliably, also during later and prolonged usage. Our aim was to achieve the best performance without restrictions and to get the best out of every cell.
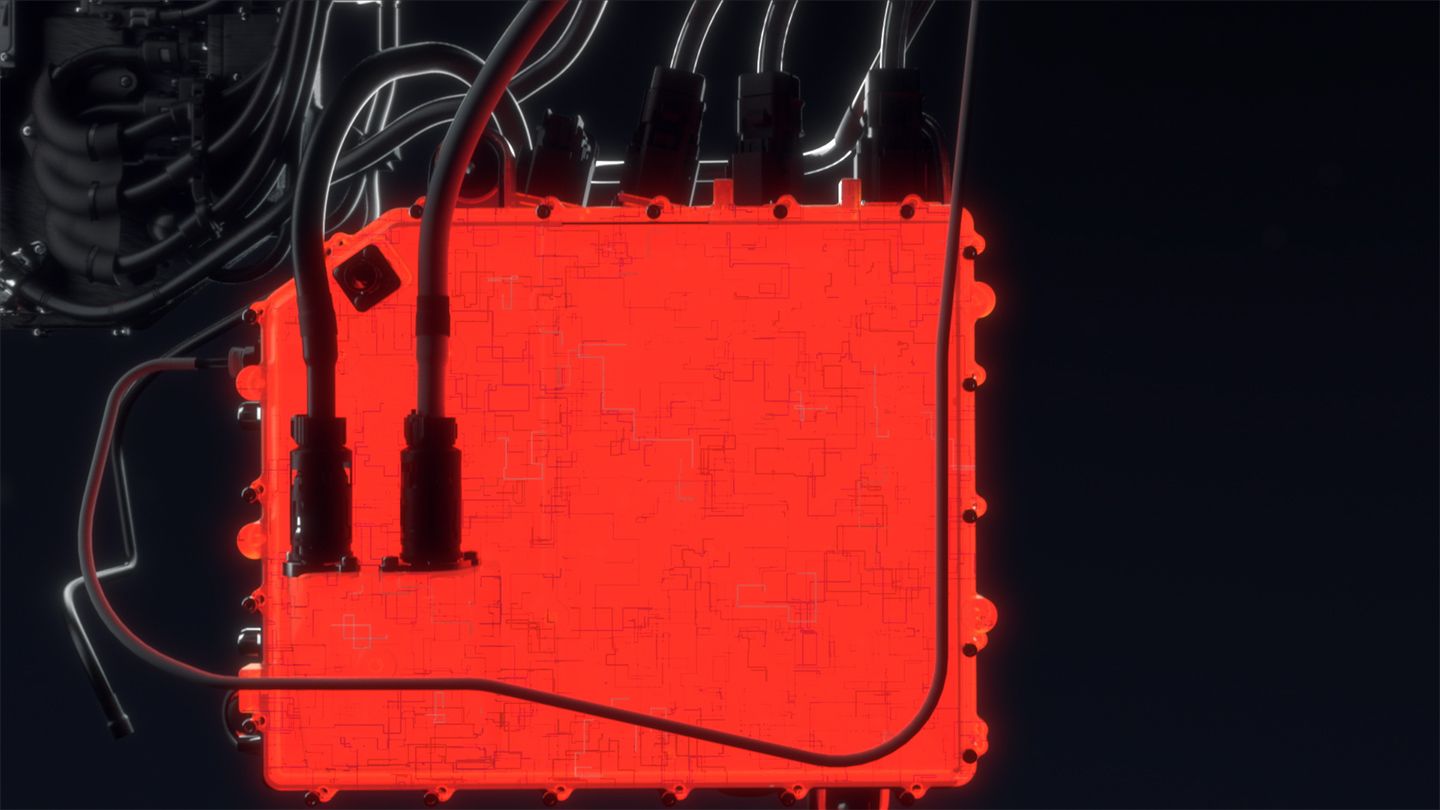
This system has been designed to be very safe in its operation, could you tell us more about why this construction is highly secure in comparison to others?
Regarding the complexity of this system; it's very important that every component does exactly what is intended and what the driver wants and expects. The front axle has two electric motors, one on each side. If the left front wheel acts inconsistently at high speeds, that’s a huge problem and could cause a crash. Regarding safety, we must prevent any irregularities or instability that could ever occur when a driver is pushing this vehicles to its limits. We have comprehensive safety mechanisms in place to avoid instability and to ensure the opposite – reliability and predictability.
The overall design is another way in which this car is very safe. Everything is located around the middle of the vehicle, including the power unit: Battery, motors, ICE, and inverters. Everything is also connected by short HV cables. All of this is protected and surrounded by the car itself. Any damage would have to be extremely serious in order to reach the HV system. In the event that such serious damage occurs, there are safety mechanisms in place which ensure that either passengers or rescue team or any other people involved are safe and able to touch the car or be nearby. The energy inside the HV system is cut and drained to prevent any electrical voltage outside.
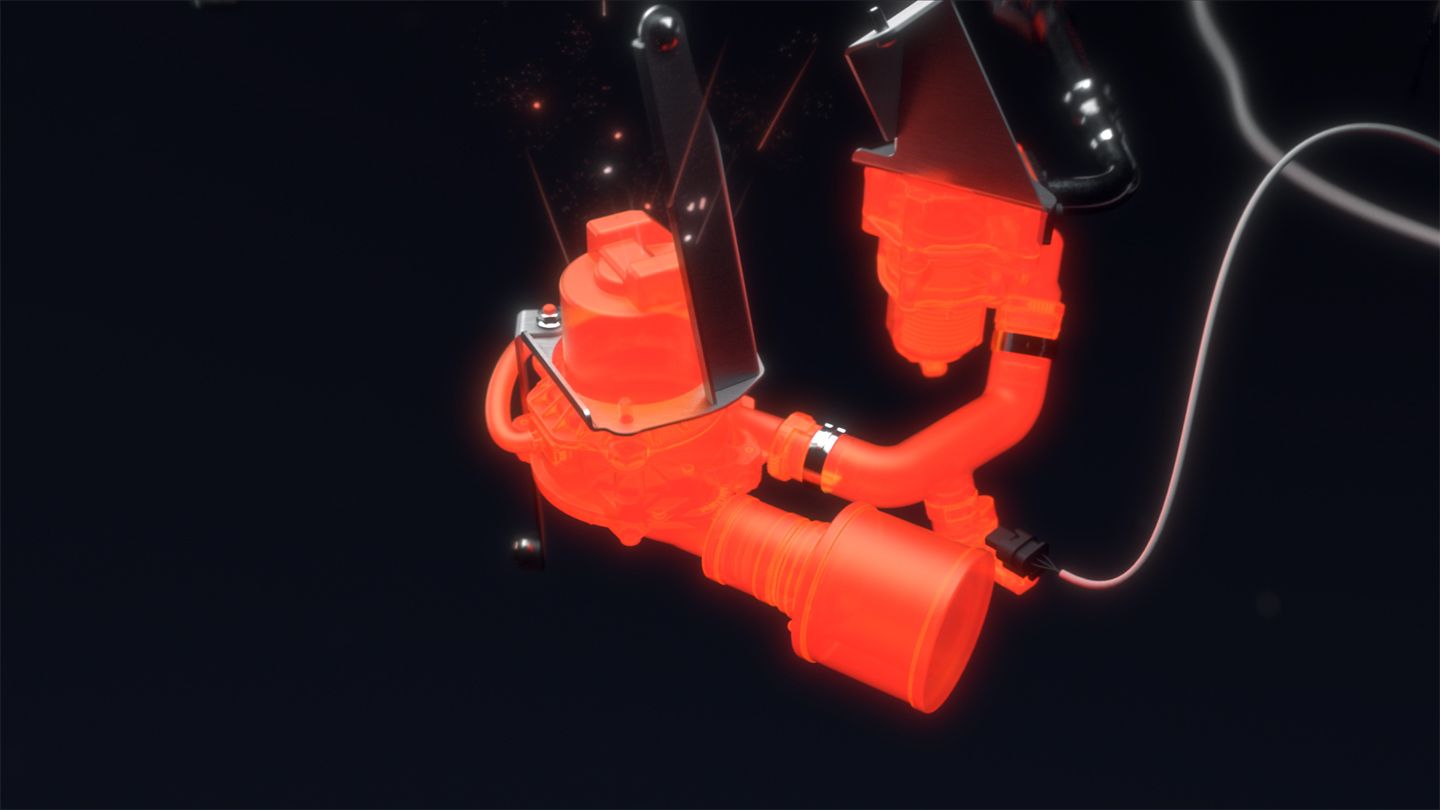
Independent of recuperation, what is the range for the electric battery system? What is the lifespan of the battery and when does it need to be replaced?
The electrical range is strongly dependent on driving behavior. Depending on ambient temperatures, battery temperatures, driving behaviour, speed on the track or on the motorway - it's pure physics that these factors drain more energy. The range varies, other Mercedes EVs operate within a range of between 20 and 100 percent. The Mercedes AMG ONE is similar. This vehicle, as a hybrid, has a much smaller pure EV capacity with its relatively small battery: Between 10-20 kilometers depending on the situation. Regarding its lifetime, this will outlast all other components in the powertrain.
That's not the limiting factor for an F1 car with a life that will easily surpass 10 years. This is also strongly dependent how it’s treated and storage conditions. Most people have observed how a smartphone battery behaves if you charge it too fast, or if you store it at extremely low temperatures with the wrong charging level, the battery will age faster. It's exactly the same here. As long as it’s treated correctly, it will live for decades, and we’ve used the best strategies in our controllers to ensure that.
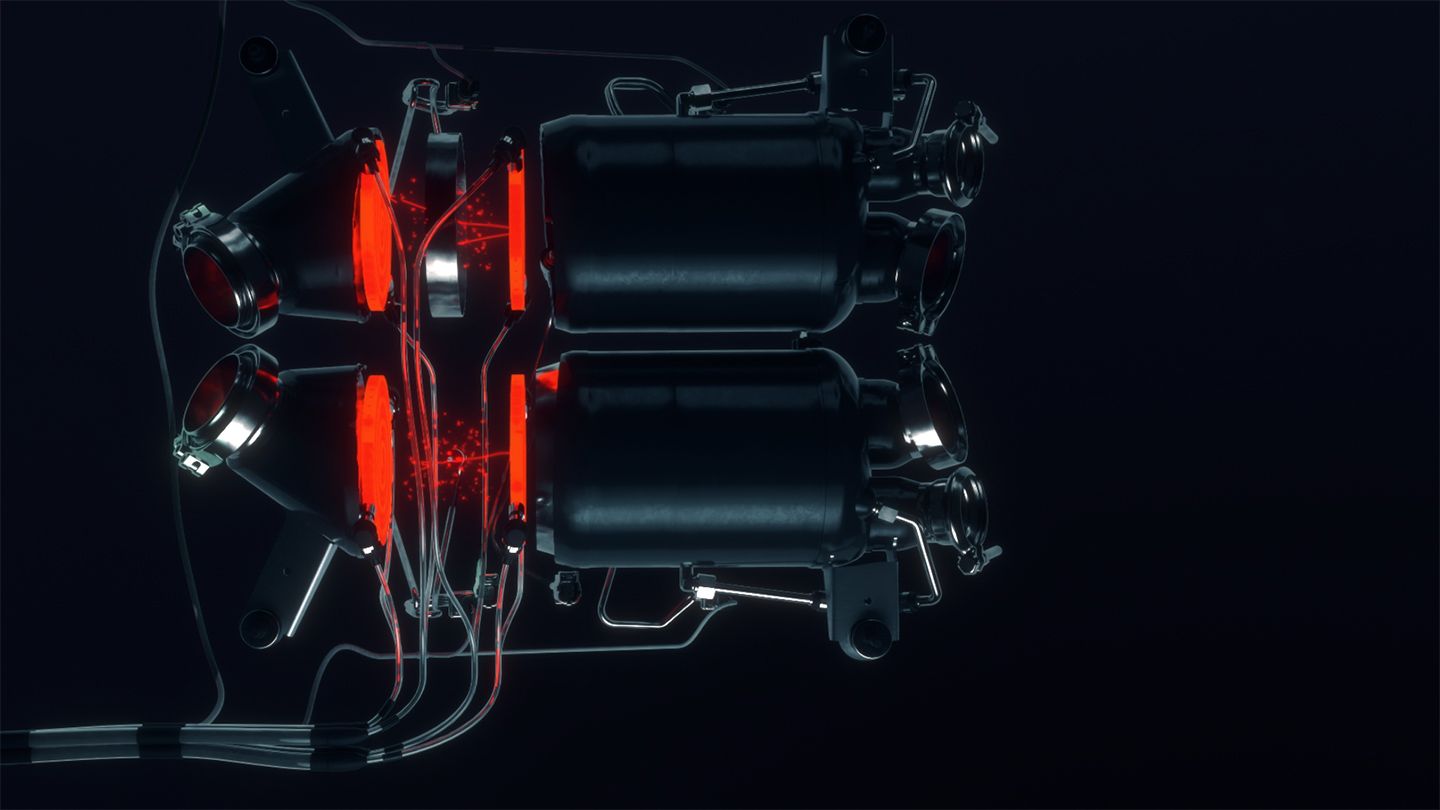
This battery system provides power to each axle, with selective power to each of the front wheels via the front-axel MGUKs – how does this power exchange/transfer feel while driving the AMG ONE? And how does this affect driving dynamics?
I haven’t yet driven the car very often, but it's an unbelievable feeling. This not only stems from the fact that we added the electrical front axle so that we can shift the torque between the front and the rear axles, it's also that we can shift the power output between the left and the right side of the car on the front axle. It’s truly an engineer's playground to support the driver. Here, you have this tool at the ready - implementing torque vectoring, which gives the driver a much more agile feeling entering and taking corners. The traction from the additional power on the front axle when exiting a corner is unbelievable.
Torque vectoring supports the driving dynamics of the AMG ONE, how does this manifest itself in this vehicle, particularly when cornering?
Torque vectoring allows the wheel taking the outer edge of the corner and the inner edge of the corner to run independently with optimum speed and optimum torque in order to support that yaw torque of the car. It feels like you're being pulled into the corner without doing anything. It’s a huge support for the driver while pushing the vehicle and each of its wheels to the limit. The result is that you get the highest cornering speed possible and the maximum traction out of that corner simultaneously and it just feels amazing.
Does this MGUH system differ at all from a Formula 1 MGUH? How much energy is recuperated in its action?
I cannot say how any other MGUH works in other F1 cars. But I personally believe that this MGUH is different to most of the other F1 engines because the turbocharger is more or less split, meaning that the compressor of this turbocharger is sitting in front of the engine, in front of the 'V' and the turbine itself is behind, and the electric motor is in between. This is a very competitive, short design for the engine overall, especially everything around the intake and the exhaust system. We've split the hot and cold sides of it, which is good for both components and for the motor in between. It’s very tricky to make that long, connecting shaft durable because it runs up to 100,000 RPM and there are always vibrations in such a component. This involved a very long development process that needed clever solutions.
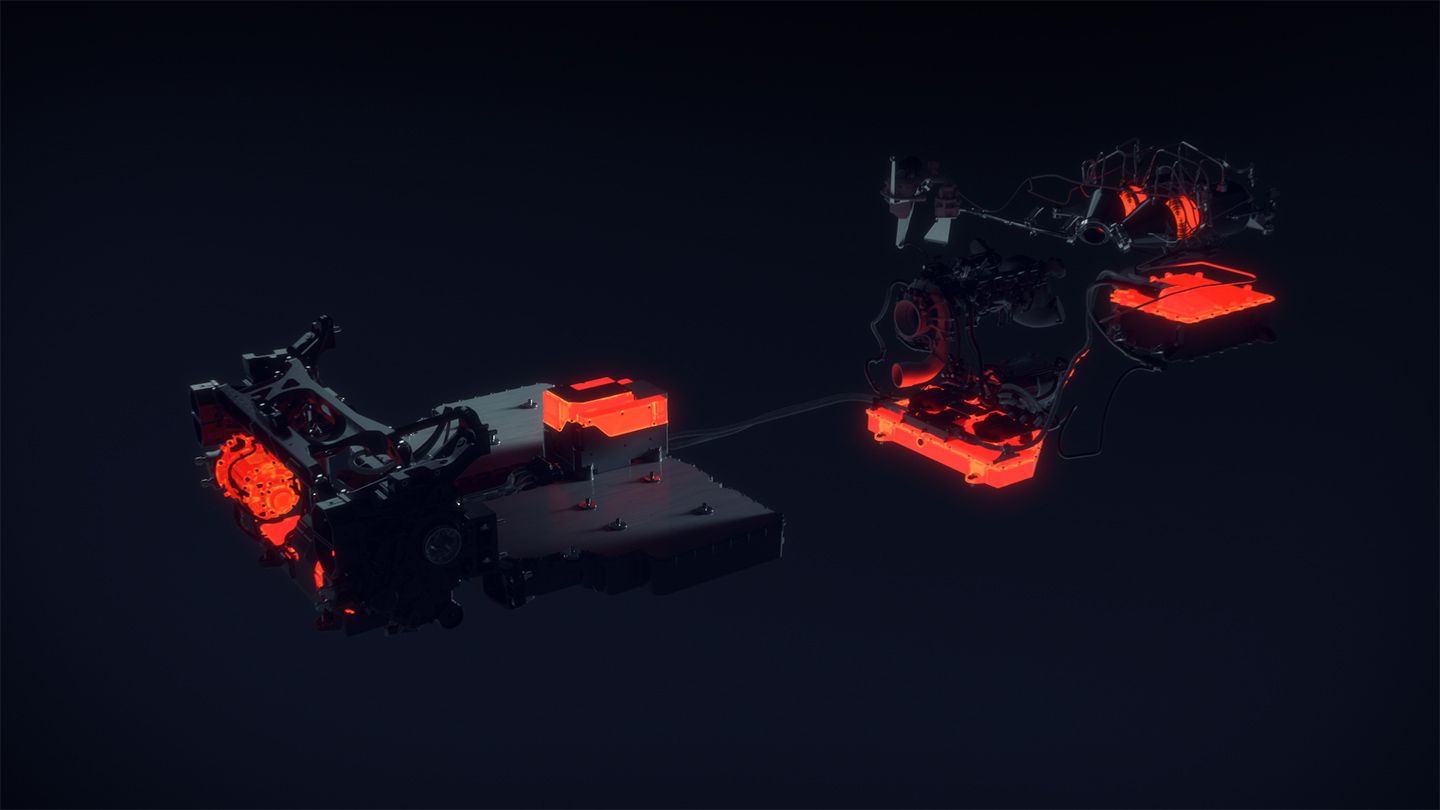
I think this development has been beneficial, especially for an F1 car. We have achieved unbelievably high efficiency, more than 80 percent, at a level never before seen from a turbine in a production engine. It’s difficult to predict exactly how much energy can be harvested under different circumstances, but more than 50 kilowatts at peak power. The average is strongly dependent on driving behavior: When running only at low revs and low torque, the result is much less than 50 kilowatts, or electrical energy needs to be deployed in order to be ready for the next tip-in so that you'll get immediate power out of it. In any case, a lot of energy can be potentially harvested and routed to either the battery or to one of the electric motors, which is the more efficient choice.
Which component is most unique and sets this battery system apart from others in Formula 1 or in the league of hypercars?
There are a few hypercars that have hybrid power trains but I think that the most differentiated element with ours is the MGUH in combination with all the electric motors. These are key to gaining this high level of efficiency, they’re the key to success. You will never see efficiency on this level in any other car. This is the first hypercar to have such a complex and efficient system.
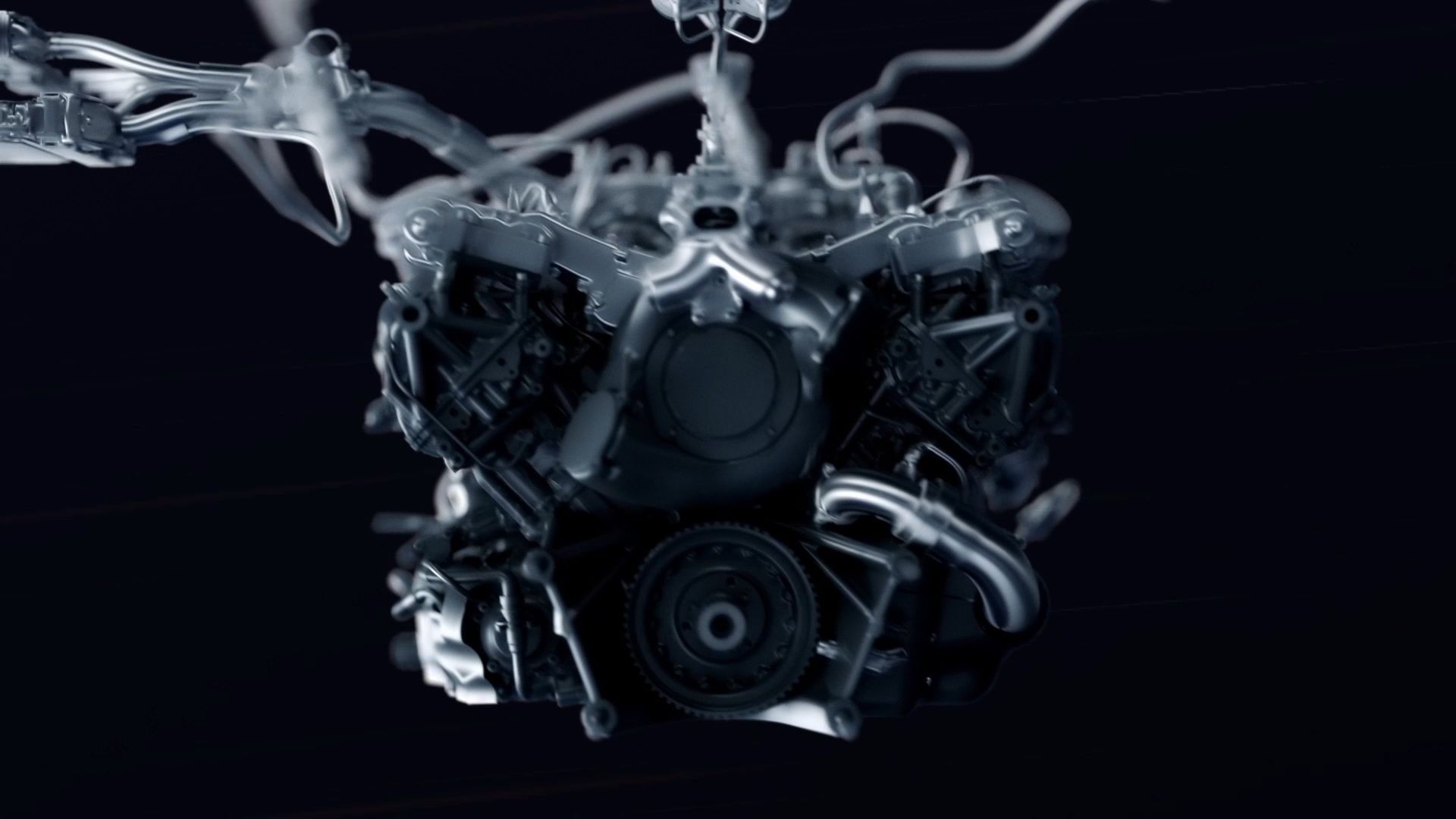
The Beating Heart of the Mercedes-AMG ONE
We were fortunate enough to speak with Adam Allsopp, Project ONE Powertrain Director, who provided us some in-depth technical insights into AMG ONE’s internal combustion engine, the story behind its development, overcoming challenges, and the power that makes this machine what it is.
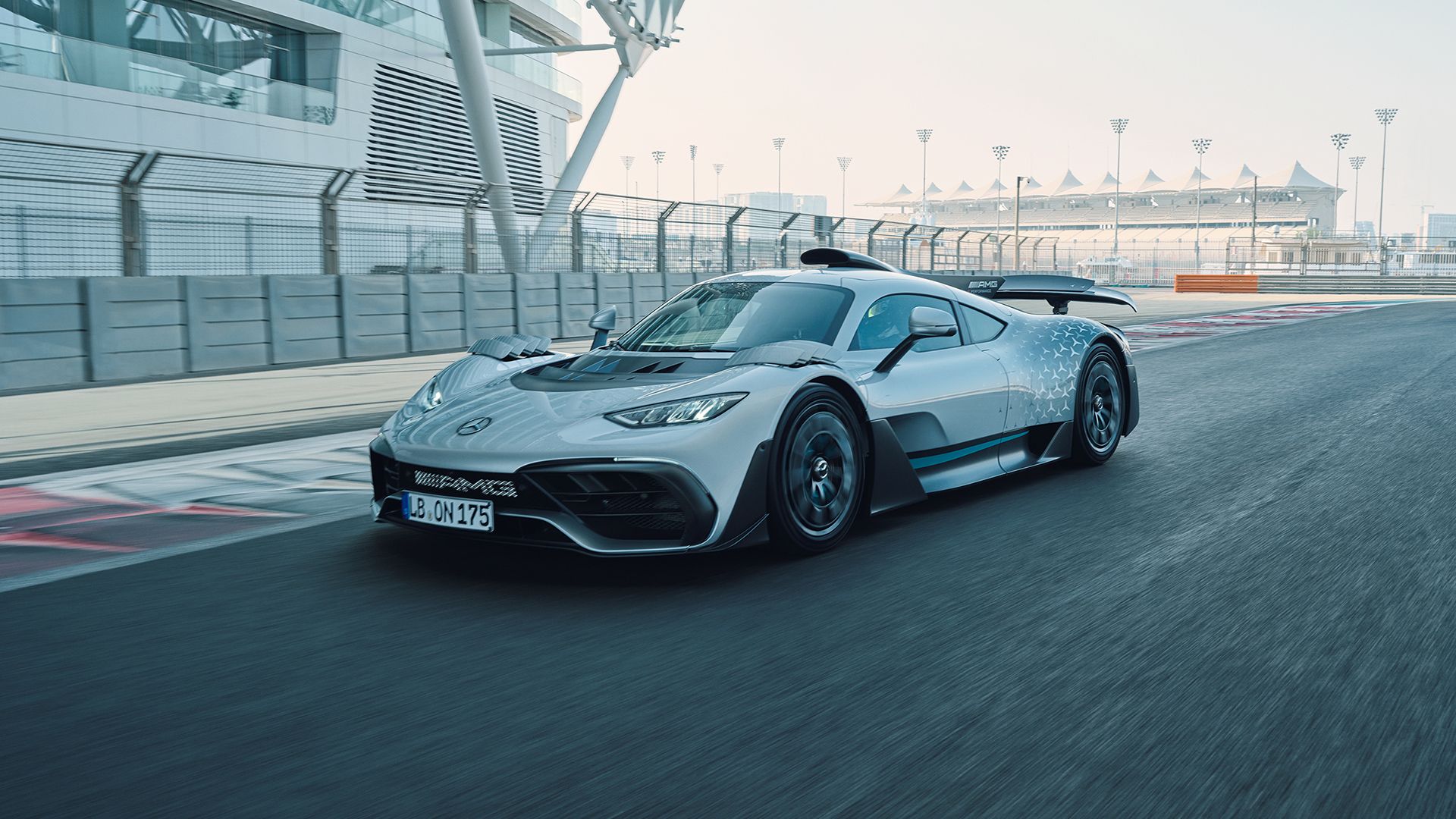
Mercedes-AMG ONE
Built to become a legend: the Mercedes-AMG ONE. The most extraordinary, contemporary, road-legal racing car to emerge from Affalterbach. Inspired by Formula 1, peppered with superlatives, made for the road.